双面电路板的制作工艺流程
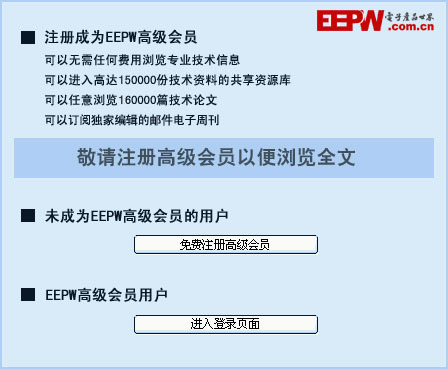
在制作双面电路板时需要准备的工具及材料大致有:双面敷铜板、热转印纸、砂纸、剪刀、油性笔、盐酸、双氧水、手电钻、烙铁、双绞线、纸胶带、烙铁、焊锡、松香等。
一、准备PCB图
1.电路原理图
以6位LED动态显示电路为例,电路原理图如下图所示。当电路图较复杂时,完工的电路图一定要经过ERC电气规则检查,采用默认选项,从而保证电路不出现短路、断路、网络名重复等严重问题。
2.PCB图
双面电路板的两面分别称为顶层和底层,顶层与底层均可布线,元器件一般放置在顶层。顶层与底层的线通过引线孔、过孔相连接,采用自动布线方式时,过孔是在布线时自动添加的。由于双面电路板的特殊性及手工制作的局限性,在设计双面电路板的PCB图时需要做如下修改:
①线径适当加宽。如普通线径Imm,电源线径1.2mm,地线线径1.4mm。在电路板尺寸允许时,线径应尽量宽并且保证地线线径电源线径普通线径。通过修改设计规则实现上述要求。另Protel DXP中的尺寸单位有英制(Imperil)与公制(MetrIC)两种,可单击【View】/【Toggle Units】在两者之间切换。例如将地线线径改为1.4mm,可单击【Design】/【Rules】,在出现的对话框中中修改Routing中的Width选项,即可将此需要添加为新的线径规则,如下图所示。
②元器件的焊盘适当加大。封装库中的焊盘的默认尺寸不适合手工制作,所以应增大焊盘尺寸。如分立元器件、集成块的焊盘直径可设置为2mm,桥堆可设为3mm,其它体积较大的元器件视情况而定。上述要求可通过整体修改实现。如将所有直径为1.5mm的圆形焊盘的直径设为2mm,ProtELDXP整体修改原理是先选取后修改。
第一步,选取。用鼠标光标指向需要整体修改的其中一个焊盘,光标要指在只有焊盘层的区域,点鼠标右键,出现鼠标右键菜单,否则,在弹出鼠标右键菜单之前还要选择是焊盘还是和焊盘连接的导线,或者器件,这时只能选焊盘(Pad)。在弹出的鼠标右键菜单里点第一项寻找相似的对象(FindSimilarObjects),弹出寻找相似对象对话框,如上图所示,我们的目的是寻找形状与尺寸均相同的所有焊盘,点PadShape(AIILayers)、PadXSize(AllLayers)和PadYSize(AlILayers)这三栏中的任意的(Any),出现下拉箭头,有三个选项分别为任意的(Any)、相同的(Same)、不同的(Dfferent),均选择相同的(Same),查找相似项的条件设置好后,点击OK,在PCB工作区内,不满足条件的焊盘均变暗,将满足条件的焊盘突显出来,并出现了检查员(Inspector)对话框如下图所示,这个对话框是工具栏式对话框,可以放在左边,也可以隐藏,出现这个对话框时选取完成。
第二步,修改。将检查员(Inspector)对话框中PadXSize和PadYSize栏目的1.5mm都改为2mm,敲回车,关闭对话框,更改完毕。现在的问题是没有修改的地方还是暗的,如何恢复呢?用鼠标点主工具栏中按钮就可还原了。用此方法不仅可快速地使所有焊盘的尺寸满足要求,还可整体修改线径、隐藏元件值、字符大小等,原理图里的批量修改与此大同小异。
③尽量在底层优先布线。双层电路板的元件放置在顶层,手工制作电路板时,由于缺少沉铜工艺,即孔壁上不能敷铜,任一个孔顶层的铜膜导线无法与底层的铜膜导线相连;插入集成器件后,器件引脚只能与底层铜膜导线相连而无法与顶层铜膜导线相连,如仍像单面板时直接焊接元器件,则电路会存在大量的断路而不能工作。如何解决呢?可先在顶层引出铜膜导线的孔中穿入过线(1~2根细铜线),并将顶层焊牢,而底层等插入元器件时与元器件管脚一起焊接;电阻、三极管等分立元器件可双面焊接,底层与顶层的线可通过器件引脚相连,因此不需焊接过线。这一部分的工作量比较大,所以在布线时应尽量减少顶层引线,采用自动布线后,再通过手工修改尽量减少顶层引线。
3.打印PCB图
通过激光打印机或喷墨打印机将PCB图打印在热转印纸上。
(1)热转印纸一面非常光滑的纸,市场上有卖,A4大小。像我们经常见到的玻璃纸、及时贴用完后要扔掉的一面,都可代替热转印纸。PCB图要打在光滑的一面。热转印纸是一次性用纸,不可多次使用,以免影响激光打印机硒鼓寿命,剩余的转印纸应保存在阴凉干燥处,不可受日光长期照射,否则影响转印效果。
(2)打印机设置①页面设置:单击【File】/【PageSetup】,弹出对话框如上图所示。颜色选择单色(mono),不能灰色(gray);比例(scaling):选择scalingprint,scale选择1.00,不能默认,否则图纸上元器件的尺寸与实物大小不相等,无法安装。其他选项可默认。
②高级选项:在上图所示对话框中单击-【Advanced】弹出对话框如下图所示,在该对话框中可以设置实际打印PCB图的哪一层,依需要删或添。
③打印顶层(TopLayer):选取多层(multi-layer,选择多层才能打印出焊盘及过孔)、选镜像(mlrror)、选洞(hole,方便钻孔及图纸粘贴)如下图所示。
④打印底层(Bottomlayer):不选镜像,其它同顶层。
1.裁板
6位LED动态显示电路的电路板大小为15cm×LOCm,电路板裁好后,先用洗衣粉清洗,后用细砂纸将边缘打磨光滑并除去敷铜板表面的氧化物,不能用力过大留下沟痕造成断线。
2.热转印
将打印好的底层图纸用纸胶带粘在敷铜板上,在电路板上空白处钻好定位孔(在PCB图中可单独添加定位孔,也可用几个分散的引线孔或过孔代替);粘贴顶层图纸时,切记要将电路板对准强光,通过透过定位孔的光线使底层与顶层图纸中的定位孔尽可能对准,这个过程称为定位。如果定位时偏差太大,元器件焊盘在底层与顶层会发生错位,错位严重时电路板无法使用。
热转印纸粘好后,怎样才能使热转印纸上的墨粉完全吸附在敷铜板上呢?由于热转印纸耐热、耐高温,并且PCB图打印在非常光滑的一面,因此当它在足够高的温度下时,墨粉将与热转印纸脱离从而吸附在敷铜板上。热转印机是实现此功能的专用设备,业余制作时可用电熨斗熨烫,温度控制在190℃左右,用力压及不同方向,熨烫大约Imin左右,效果也可以。切记当敷铜板完全冷却后,才能撕去热转印纸。
如果担心电熨斗加热的效果不好,手工制作时还可采用另一种方法。将顶层与底层的PCB图打印(任何打印机均可)在质量较好的及时贴上,质量较差的及时贴背面的胶粘不牢,腐蚀时易脱落。用与上述相同的方法将顶层与底层图粘贴在敷铜板上,再用直尺与小刀配合去除连线、焊盘除外的多余的纸,最后要清理干净残留在敷铜板上的胶,否则会影响腐蚀速度及效果。这种方法不需任何特殊设备且效果好,缺点是电路复杂时,费时较多。
3.补线
不论是用热转印机还是用电熨斗热转印后,都会或多或少存在某些断线,不要担心,可用普通的油性笔对照PCB图进行手工修正。
三、腐蚀将
修正后的电路板,放到盐酸+双氧水+水(1:3:7)的腐蚀液中,这种液体清澈透明,可清楚地观察电路板的腐蚀程度。在腐蚀过程中要注意安全,选择通风好的地方,带上手套。约数分钟后,即可得到做工精细的双面电路板,记得要用清水洗去残留的腐蚀液,但不要清理掉墨粉或及时贴。
四、钻孔
使用手电钻或小型台钻进行钻孔,可先钻过孔、分立元器件的引线孑L,手顺后再钻集成电路等要求高的引线孔。由于某些孔内需要穿1~2根细铜线才能将某一引脚底层与顶层的敷铜相连,所以可采用比平时稍大的钻头,如0.9mm,孔径太小时,集成块插座不易插入且过线易断。
钻好所有的孔后,用细砂纸或洗衣粉清理干净剩余的墨粉或及时贴。电路板终于制作出来了,下面就是电路板的焊接了。
五、电路板焊接
1.检查
由于是手工制作所以在焊接之前,通过肉眼观察或万用表测量,看是否有断路或短路,及时修正,重点检查顶层有无短路,因为元器件安装在顶层后,将某些引线覆盖,如果存在短路,检修起来会特别费时。
2.焊接过孔
双面电路板较复杂,焊接时一定要有一定的顺序,一般先焊接所有的过孔,由于设计PCB图时,过孔与元器件焊盘的尺寸不同,很容易区分,焊接时在过孑L中穿过1~2根铜线或0.5mm的硬芯线,顶层与底层都焊牢后,剪去多余部分。
3.焊接过线
为使顶层整齐美观,不使用双面焊接,因此顶层所有引出铜膜导线的引线孔内均要焊接过线,为了避免短路,顶层过线压平后要与引线孔引出的铜膜导线走向一致,在离引线孔Imm处焊牢;而底层不需焊接,预留lcm后剪去多余部分。
4.焊接元器件
过孔与过线焊接完后,下来就是焊接元器件了,一般是根据元器件的安装高度从低到高依次焊接。重点是集成块插座,插入时要对准所有的孔后,均匀用力下压,注意不要将孔内的过线弄断,然后将底层预留的lcm过线提起,与引脚并在一起焊接后并剪去多余部分。
六、通电测试
通电前检查有无漏焊、虚焊、错焊,并用万用表测量电源与地之间的阻值,阻值过小时可能存在短路情况,排除后再通电测试能否实现预期的功能。
评论